|
Am I the best stained glass artist? One of
my close friends would often introduce me as one of the ten best
stained glass artists in the world, and I would counter that if I was
truly among the best, I probably would have gotten rich making stained
glass.
But maybe I am one of the best stained glass artists. Very often, I get
to the middle of a project and think, "It's a good thing these clients
chose me because I don't know of any stained glass artist who could do
this project this well." The residential office doors you see above are
a good example of this. Very few stained glass artists have the right
attitude or go to the trouble I do to make leaded stained glass look
this good.
Precision work has always been the main focus of my stained glass work.
Although I never make a perfect artwork, I try to improve my skills
with every project I undertake no matter how large or how small it is.
That is also why I have produced a 43-hour set of DVDs
to teach what I know to other stained glass enthusiasts.
These doors include bevels made by one of the best bevel makers I have
ever found, Action Bevels.
Still, bevels are hard to work with.
First because bevels, like all geometric designs, should be
leaded, not copper foiled, and working with lead came is harder than
copper foil, which is why 99% of beginners are taught copper foil and
many are not even exposed to working with lead came. (There is nothing I think is
uglier in the
field of stained glass than copper foiled bevels!) And
second, because
bevels are made by someone other than me, working them into a project
requires significant extra effort. In my work, this means laying out
the
bevels on the full size drawing, one bevel at a time. By starting with
the center
bevels and working outward, and by grinding the edges of each bevel
until
the fit is perfect, I am able to get the proper precision fit. Then, I
trace around the bevels so that the stained
glass background pieces that surround the bevels will also be as
precise as
possible. Even still... even including all this extra effort, leading
together a beveled project usually requires some changes to make it
come out right. In this project, for example, I had to grind a few of
the blue glass pieces that separate the beveled pieces, making them
just slightly thinner so that the last few beveled pieces would fit
into place.
So while these beveled and stained glass panels are not perfect, maybe
they are as good as it gets and maybe that makes me one of the very
best stained glass artists.
The photo above, taken by the clients, is a very good photo (st gl is
incredibly hard to photograph well). But the pink glasses I used in the
flowers and in the thin inner border look a bit washed out, so I am
including the photo below that a friend took just after I had finished
one of the panels (and prior to darkening the lead and solder with a
special patina).
There
is one more noteworthy aspect to this project. I don't have
repeat
clients very often, but this was one of the more interesting times that
I did. Years ago, I made a stained glass panel to be mounted in this
couple's pantry door.
They liked it so much that they took it with them when they moved into
a new home they had just built. They asked me to enlarge their existing
stained glass so it would fit into a larger opening in their new pantry
door. That meant they would have to ship the panel to me, and the plan
was that I would ship all three panels back to them. There is some risk
in shipping although it comes out fine most of the time. There is also
a significant cost to wood-crating and insured shipping for large
panels such as these. So we came up with the plan that after I had
completed the two office door panels, they would drive the pantry door
panel to me (from Tennessee!) and I would enlarge it while they visited
family about an hour from Denver. Then they would drive all three
panels back home. The plan went smoothly, and they even came
with a wood crate they had made that would hold all three
artworks.
At one point, a friend of theirs asked why they would drive all the way
from Tennessee to Colorado to do this... wasn't there someone closer to
home that they could commission to do this? After the panels were
installed, that same person commented that they now understood why,
that these panels were clearly worth going all that way.
When I finish a project, I post it on my facebook page. The most common
response to this particular project has been "Wow! Amazing stained glass!"
The positive feedback I get from being good at stained glass never gets
old. I may not have gotten rich in life making the "best" stained
glass, but I like my life a lot just the way it is.
Once I begin a project, I email progress photos to the clients while I
am making their
artwork. Clients love this, and it's not hard to do. Below are some of
the process photos I sent this couple while making these door panels.
They show the precision craftsmanship that goes into every
great stained glass artwork I make.
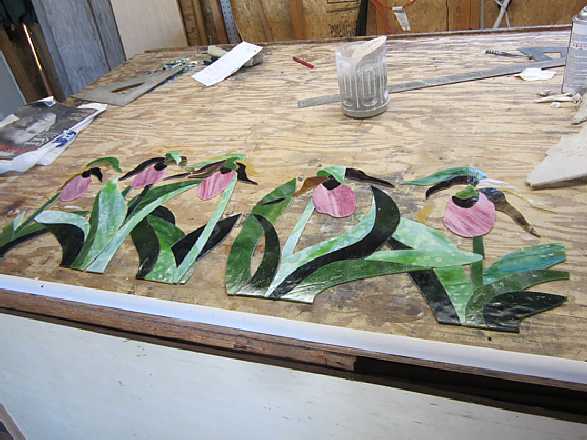
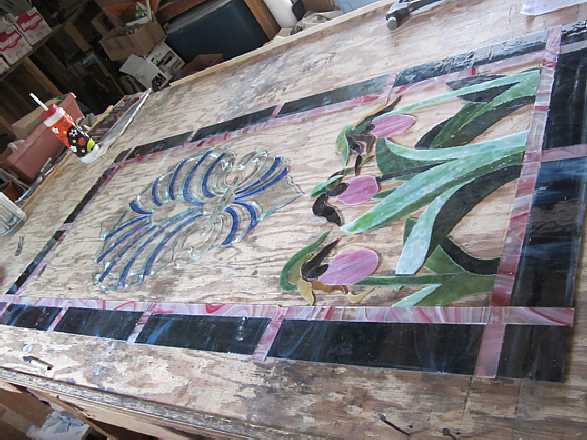
To
give this artwork enough internal strength (allowing me to avoid
unsightly steel reinforcement bars soldered to the backside of these
panels), I replaced the lead came with zinc came for all of the leadlines in the border. These
long vertical lines of uncut zinc avoid the tendency for stained glass
panels to bow out of the vertical plane along horizontal lines in the
design.
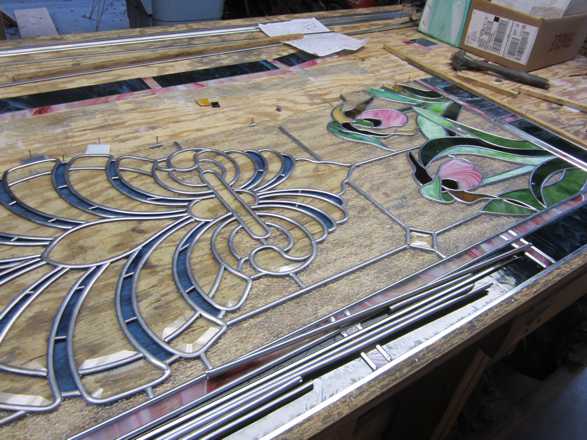
|
Return to the gallery
|